
3D Print Recycler - Filament Collection
Design and fabrication of a collection system used to spool polymer extrusions to allow the recycling of 3D printed ABS parts.
Goal: Create a system which can collect an extruded polymer melt.
Scope: Generate and fabricate and design to allow the polymer melt to be collected and spooled within the Capstone project budget.
Constraints:
A total Capstone budget of $5,000, of which a small minority was dedicated to the collection system.
The polymer melt must be cooled below the glass transition system during spooling.
The final spooled filament must be a usable diameter within 3D printers - our goal was the industry standard of 1.75mm.
Collect the filament onto pre-existing filament spools which would otherwise have been discarded.
My group project for our Mechanical Engineering Capstone was to create a system to allow 3D printed parts to be recycled into spools of filament for re-use. This is especially important in a university environment where many parts are being printed soley to learn how to use 3D printers without a final end use.
There were three major components of the system design - the shredder, extruder and collector.
Shredder - Break down the 3D printed parts into small pellets.
Extruder - A twin-screw, heated extruder design which reduced the pellets into a polymer melt.
Collector - A winding motor driven system which spools the polymer melt, allowing it to cool.
The collector was of my own design. Using a small 12 VDC gearmotor wired in series with a regulator, we were able to adjust the draw speed of the collection system. The system was powered using a 12 VDC power brick with a barrel connector. This draw speed allowed us to adjust the final diameter of the collected filament for various 3D printer extruder heads.
Project Gallery
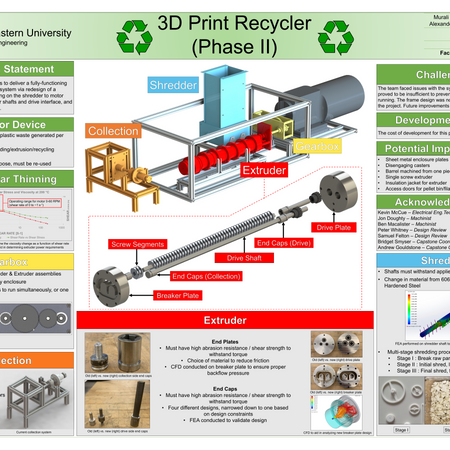



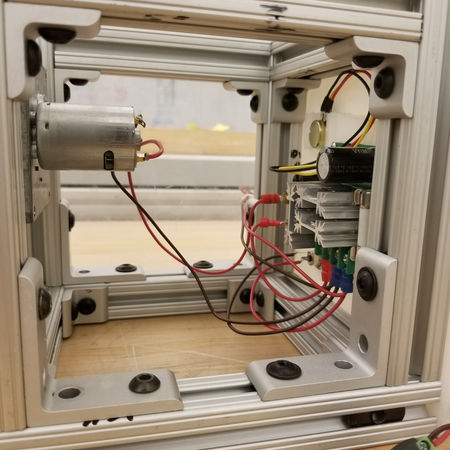
